Long distance RDF conveying and dosing
Long distance RDF conveying and dosing
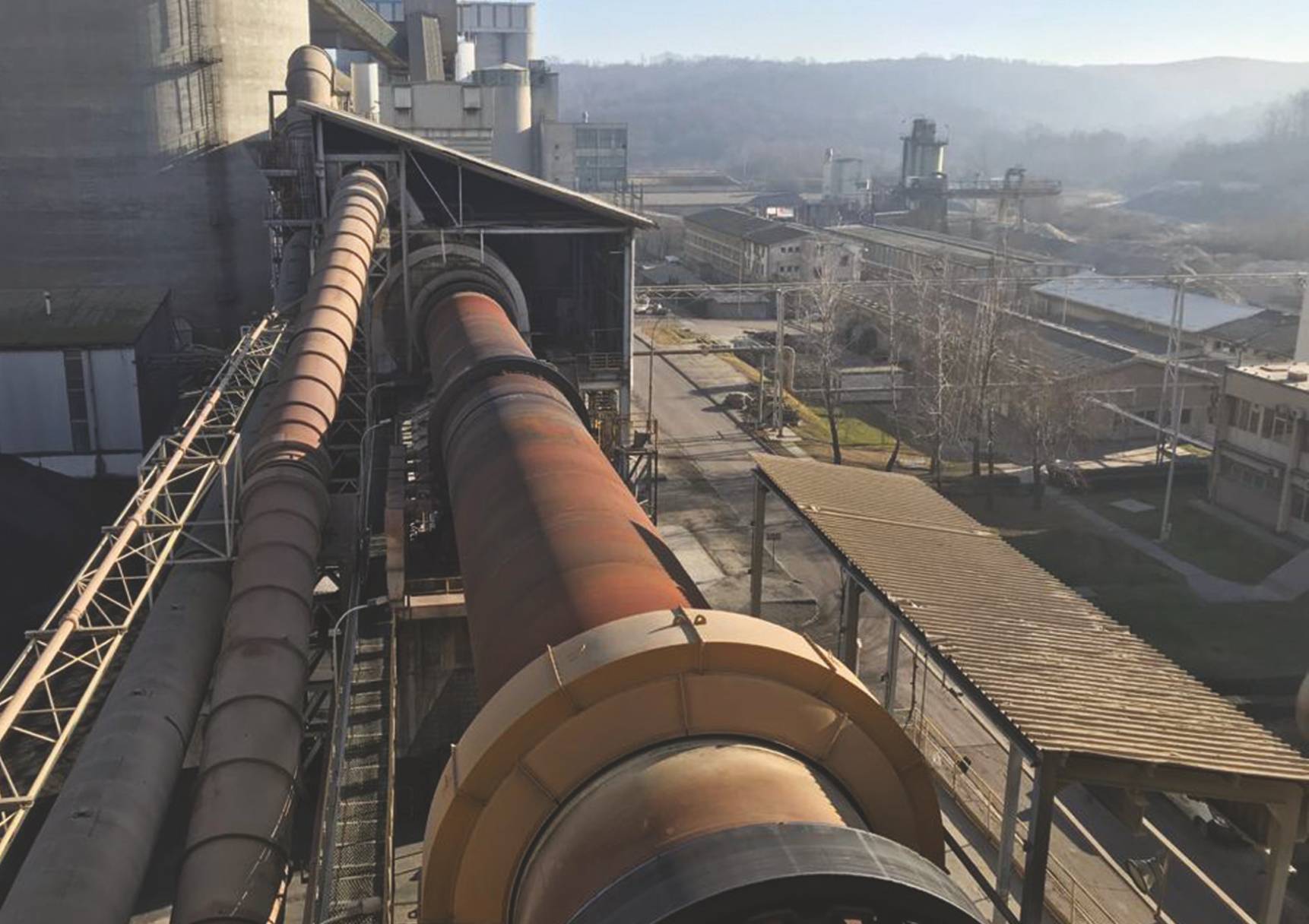
With the introduction of alternative fuels into the calciner being relatively more technically challenging than into the main burner of the kiln, ERITECH developed a dosing solution for the calciner of NEXE ddʹs Našice cement plant that involves one of the longest pneumatic transport lines for refuse-derived fuel in the world. Thanks to the project, the cement producer has been able to take advantage of additional RDF in the regional market
Alternative fuels (AFs) are an increasingly popular replacement for fossil fuels in the cement industry. One of the tried-and-tested approaches in the use of refuse-derived fuels (RDF) in combination with various other AFs such as waste oils and waste gases. These sources may reduce or completely substitute coal dust, natural gas, or oil in the main burner not only in the kiln but mainly in the calciner. ERITECH has developed a unique solution for dosing RDF at the calciner of NEXE ddʹs Našice cement plant in Croatia, which encompasses one of the longest pneumatic transportation lines in the world. The project challenges the usual deployment of conveyor systems, while saving capital, reducing installation time and minimising the need for supporting civil works.
Refused-derived fuel to the calciner
Due to legislation changes concerning waste management and increasing landfill fees, the availability of quality RDF has increased. There have also been advances in the processing, production and refinement of RDF. This combination of factors has led to an increase in demand from cement producers for RDF in the production process, including in the calciner. The feeding of AFs into the calciner is technically more challenging than feeding them into the main burner of the kiln. The key reasons for this are demands in terms of combustion optimisation, required material handling, dosing equipment, in addition to limitations of the available area for the installation and structural limits of the calciner tower. This is especially applicable in older plants that have various other auxiliary equipment and structures installed in the surrounding area of the calciner tower that leave little available space.
Standard mechanism implementation is time and financially demanding
Traditionally, the mechanism for transporting and dosing RDF to the calciner are a conveyor and weight-controlled dosing equipment. Most belt conveyors have a main limiting factor of a 20° inclination, and in the case of tube belt conveyors the inclination may be increased to 30°. This requires the horizontal distance between the point of loading and unloading to be approximately 175 per cent more than the vertical distance between these two points. In such a case, additional civil and structural supports are essential. Furthermore, the conveying system is usually coupled with a large storage system. Utilising RDF in the calciner using the traditional approach is considered a large financial investment and it time-consuming to implement. Thank to the ERITECH solution for dosing RDF to the calciner, the customer was able to take advantage of the additional RDF in its regional market. As the kiln main burner was already operating at maximum RDF consumption, the optimisation project created a new way of utilising this valuable resource.
ERITECH designed and produced one of the longest RDF pneumatic transportation lines in the world
ERITECH designed and produced a pneumatic line with over 220 metres of pipe, comprising 43 vertical metres, 170 horizontal metres and 14 metres in bends, including five 90 degrees bends and two 170 degrees bends. This served to connect the distance between the existing RDF dosing system and the calciner. In the operation of the line, ERITECH had to ensure that the RDF was separated from the transport air before entering the calciner. This was essential for maintaining the thermal performance of the calciner. However, with this combination of air and fuel mix, the design needed to be explosion proof.
In the new installation, the existing intermediate storage with weight-controlled dosing for the kiln´s main burner has been modified and expanded with an additional weightfeeder. The storage area is located approximately 70 metres from the kiln main burner. The newly installed weightfeeder is the main dosage control equipment and prevents overloading of the pneumatic feeding system as well as metering the fuel input to the calciner.
The weightfeeder doses to a blow-through rotary valve from where the pneumatic transportation begins. The pneumatic line is classified as dilute (light) phase conveying and is powered by a rotary lobe (Roots) blower operating at 900 mbar and producing up to 3300 m³ per hour of conveying air. From the blow-through rotary valve the RDF is transported to a cyclone located on the near upper level of the calciner. ERITECH designed the cyclone specifically to separate the RDF from the pneumatic transport air. The use of the cyclone is crucial to maintaining the thermal performance of the calciner. While the main burner uses transport air as supporting combustion air, this is not required in the calciner as the necessary amount of oxygen is already available. This transport air is also “cold” and at this large quantity (up to 3300 m³/h) its introduction into the calciner would have significant thermal losses.
Therefore, a cyclone is utilised to separate the solid RDF material from the air. The cyclone is specifically designed to accommodate the large and varying particle sizes typically found in RDF. Its dip tube is longer, and its lower cone was removed, so the outlet does not become clogged as RDF has tendencies to bridge in narrow cross-sections. Additionally, there is a larger transition inlet to allow for necessary expansions and decelerations of incoming RDF.
The dirty air from the cyclone is filtered by a bag filter to remove any dust or other small RDF particles before they are discharged to the atmosphere. This bag filter is equipped with a hopper and collecting screw conveyor. From the collecting screw conveyor, the RDF dust in reintroduced back into the system via a small rotary valve. The rotary valve serves as an airlock between the filter and feeding system.
From the cyclone the RDF drops directly into the top of a material splitter. The material splitter is a double bi-directional (reversible) screw conveyor with a small volume hopper located in the centre. The screws are parallel to each other and operate with independent frequency converters to maintain various rpm set points and reverse the rotational direction of the screws. This allows material to be proportioned into two different material streams. During normal operation, the screws rotate at the same speed and in opposite directions. This mode delivers equal amount of material to both outlets. By controlling the speed of the screws, the material can be divided from 10–90 per cent between the outlets. Additionally, the screws can operate in the same direction and feed 100 per cent of RDF to one outlet.
Below each outlet of the material splitter is a short chute followed by a large rotary valve. These rotary valves are some of the largest available on the market in an ATEX explosion-proof design. The rotary valves serve two purposed. Fist to function as an airlock to prevent both the pneumatic transport air from entering the calciner and hot flue gasses from entering the feeding system in case of process swings or backflashes. After the rotary valve there is a direct chute to a splash box that is connected to the calciner directly above the smoke chamber. Secondly, and more importantly, these rotary valves are of an explosion proof design and provide a barrier between the risk of explosion area and the non-risk of explosion area.
An explosion-proof design
RDF transportation over more than 200 metres requires high velocities. At such speed, there is explosion risk due to the dust generated in conjunction with the potential for static electrical discharges and sparks produced by metallic collision withing the system. Therefore, ERITECH designed the entire solution to be explosion-proof. In this respect, the pneumatic transport pipe, cyclone, filter (including hopper and screw conveyor), material splitter and rotary valves were manufactured in +500mbar explosion proof design. Another component to mitigate the risk of explosion is an explosion detection and suppression system. This system uses pressure sensors to detect rapid increases in pressure. In case of an emergency, the system deploys a chemical suppression to prevent continuation of the explosion within the closed environment.
Pneumatic transport using cool air
ERITECH applied another method to reduce the risk of explosion by significantly lowering the pneumatic transport air temperature. In general, the heat generated by the rotary lobe blower and through the process of compression leads to air discharge temperatures which can exceed 125°C (at 40°C atmospheric inlet). In the solution, the discharge air is reduced to less than 10°C above the inlet atmospheric temperature, e.g., a 20°C inlet will have an outlet temperature of <30°C. This was accomplished by utilising an aftercooler, which is an air-to-air heat exchanger with forced flow cooling. This aftercooler is connected between the blower discharge and the inlet of the blow-through rotary valve. Having cooler transport air not only reduces risk of explosion but also provides longevity and component cost reduction by selecting standard components such as bearings, lubricant, seals, filter bags, etc., which are rated for operation below 60°C. Furthermore, a lower transport air temperature is beneficial for reducing the chances of clogged transport pipes due to the high concentration of plastic found in RDF. At higher temperatures plastic becomes more malleable, which can lead to material blockages in the transport pipe.
Short timeline
During the installation of the conveying solution, ERITECH acted under time pressure to enable dosing of the RDF in the shortest time possible. This was another reason why a traditional conveying and dosing system would not have been practical. The entire pneumatic transport line and dosing equipment was installed within less than a year and between the annual shutdowns.
Solution for the future
ERITECH together with NEXE dd consider this project a success, and the entire project – from conceptualisation to commissioning – was undertaken in just seven months. NEXE dd is now able to capitalise on the RDF market and reduce its consumption of fossil-based fuels. This project was carried out efficiently and with a future capacity increase in mind by sizing the relevant new mechanical equipment for a feed rate capacity increase, so that when time permits, a traditional belt conveyor system can be easily installed while only requiring a short downtime for implementation.
Source: International Cement Review
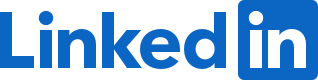